When looking for an epoxy coating for your project, you need to know a little about the different types. There are a number of different types of epoxies, but the most important difference is their molecular structure. In this article, we will talk about Phenoxy, Bisphenol-A, Dioxane, and Polyurethane. These are the four most commonly used types of epoxy. Listed below are the differences between them, but to be sure, consult an epoxy floor contractor.
Polyurethane
There are a variety of differences between polyurethane and different types of epoxy, but these two common coatings all have the same purpose: to create a durable and aesthetically-pleasing coating. Epoxies are tougher and more durable, but polyurethanes offer greater aesthetic versatility. They come in different colors and sheens ranging from amber to crystal clear. Both can be water or oil-based. The higher the sheen, the more durable the coating.
While epoxy and polyurethane are both waterproof, polyurethane is more flexible. Its paint coating contains plasticizers that allow the film to stretch and contract with temperature changes. Epoxies, on the other hand, are extremely hard and brittle. Another difference between polyurethane and epoxy is drying time. Water-based polyurethane dries within two hours, while epoxy takes about 24 hours to dry.
In general, polyurethane has more advantages than disadvantages. Oil-based polyurethane can be thinner and used as a wood sealer. Water-based polyurethane is more flexible and can withstand high relative humidity. But in humid environments, polyurethane may have lower durability. In most environments, epoxy has a longer service life. Therefore, a decision should be made according to the application and the environment.
Compared to epoxies, polyurethanes have a higher cross-link density. As a result, they are more durable and can incorporate antimicrobial additives to prevent bacteria from growing. It can also be installed at different depths and levels and can be used on uneven floors. A polyurethane coating is easy to clean and long-lasting. It is available in both water-based and oil-based formulas.
Phenoxy
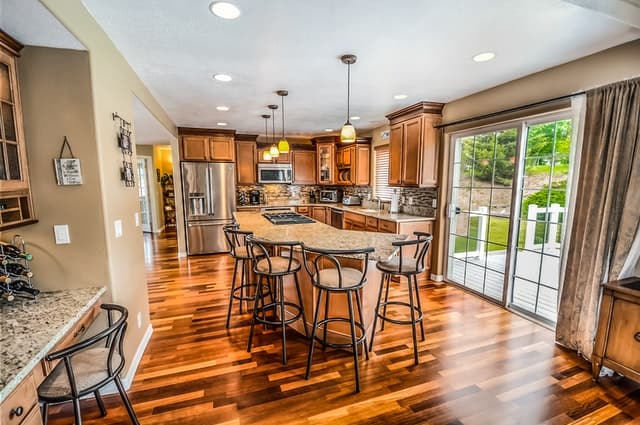
Epoxy is available in two components: the hardening agent and the epoxy itself. They are mixed thoroughly to create an exothermic reaction that begins the curing process. Different curing environments result in varying cure times. Some can be applied at room temperature while others require a higher temperature to fully cure. A two-component epoxy will take two to three hours to cure but will cure much faster with additional heat. Regardless of the type of epoxy used, you should follow the directions carefully and follow the manufacturers’ recommendations.
The two most common types of epoxy are glycidyl and non-glycidyl. The former are ethers and amines with an aliphatic structure. Non-glycidyl epoxy resins are cyclo-aliphatic or aliphatic. While the former is generally considered to be the best choice, some applications call for a specific type. Non-glycidyl epoxy is available in a wide range of properties.
Two-component epoxy resins are easy to use. They are easy to mix and apply to a variety of materials. Two-component epoxy has a wide range of uses, and a one-component resin has some advantages that depend on your application. Both types are effective in various types of projects. However, if you’re looking to repair a remote control airplane, liquid epoxy may be the better choice. In contrast, slow-drying epoxy will allow for precise part placement and more time for curing.
Dioxane
Dioxane is a clear liquid with a faint ether-like odor and is easily flammable. This chemical is commonly used as a stabilizer for paint and varnish, a paint stripper, and as a laboratory reagent. While dioxane is not carcinogenic, it is a trace contaminant in cosmetics. For this reason, it is recommended that you avoid its use.
In The Netherlands, 1,4-dioxane production stopped twenty years ago, but its migration into the groundwater continues and poses a threat to surface water. To help prevent the spread of dioxane, the company installed modified TreeWell(r) units in the soil. By early 2013, 240 poplar trees had been planted in the area, and they showed excellent growth. The dioxane plume is drawing into the planted area.
The chemical composition of cured epoxy resins with GEC is presented in Table 1. The presence of GEC induced a marked increase in Char800 values of the DGEBA-cured resins. Similarly, the addition of GEC to DGEBA resins reduced resin decomposition. The two-part mixtures were then cured under nitrogen for 24 h. At this temperature, the samples showed better thermal stability and char yield at 800 degrees C.
There are various ways to biodegrade 1,4-dioxane. One method involves using propane sparging to promote bioaugmentation. Once the bioaugmentation process with Rhodococcus ruber ENV425 began, the concentrations of 1,4-dioxane decreased from 0.21 to 0.036 ppm and increased from 0.05 to 0.05 ppb/min.
Bisphenol-A
In addition to being a strong adhesion agent, epoxy Bisphenol-A resins can have a range of beneficial properties, including their ability to resist water. These compounds are also mutagenic and may cause allergic dermatitis in some people. The Japanese Ministry of Health, Labor, and Welfare has established official handling guidelines for Bisphenol-A resins. However, these guidelines are general in nature and may not be sufficient for your particular situation.
To create liquid epoxy resin, bisphenol-A is combined with epichlorohydrin. The two chemicals react, releasing a hydrogen and chlorine atom. Afterward, the epoxy resin is formed. This liquid type contains relatively few repeat units, whereas the solid epoxy resins contain two to 30 units. Bisphenol-A resins are a popular choice for a range of applications in the electronics industry.
Micrographs of various blends show a high degree of crystalline structure, with the dark regions representing the polybutadiene phase. Its OsO4-stained morphology indicates that the epoxy chains penetrate through the rubber domain, but the ratio decreases as the concentration of the polybutadiene increases. The same goes for thermosets with more than five percent PBNCO. When the rubber content increased, the amount of polybutadiene in the thermoset decreased, and the number of rubber domains increased.
Polyamides are another type of epoxy resin. These resins contain polyamide backbone aliphatic chains joined together by amide linkages. These components are excellent for machinery applications because they are highly elastic. They can also be combined with epoxy Bisphenol-A for a stronger, more durable coating. The polyamide resins are more abrasion resistant and offer excellent adhesion to substrates. This type of epoxy resin has many beneficial properties and is a good choice for many applications.
Vinyl Acetate
Various industries use vinyl acetate in different ways. Its use in various types of adhesives and paints is significant. Additionally, it is used in textile treatments and paper coatings. The market for vinyl acetate is growing in the Asia Pacific, with the region expected to post the highest CAGR over the forecast period. Moreover, the demand for this substance is expected to increase further due to various government initiatives.
While vinyl acetate is very toxic to human health, it is readily distributed in the body and breaks down rapidly. It leaves the body only in trace amounts through the urine and waste. This is why U.S. Occupational Safety and Health Administration has set certain limits for worker exposure. However, these limits are not arbitrary. They are intended to limit the potential risks of vinyl acetate exposure. But these limits may not be sufficient for all applications.
Another important component of the plastics industry is vinyl acetate. It is used in adhesives and is a significant component of wood glue, white glue, and carpenter’s glue. Other applications include laminated safety glass, construction materials, and packaging films. In addition to its use in adhesives, vinyl acetate is also used in various types of packaging films. They have excellent adhesion properties and are also used in plastics and paper coatings.
UV Resi
The advantages of UV resins over traditional epoxy are numerous. UV resins don’t require measuring ratios or long curing times. UV light or sunlight can cure them in minutes and give them a hard, glass-like finish. The PREMIUM Crystal Clear UV epoxy resin has self-leveling and de-gassing properties. It also cures a glass-like finish without any bubbles. Its spout is easy to use, allowing the user to pour a precise amount of resin without having to adjust the ratio.
You can purchase UV resins online or at stationery stores that sell equipment. The resin is relatively inexpensive compared to the UV lamp, which can be expensive but only pays for itself if you’re using it regularly. To mix the UV resin, you must first prepare a mold and a light source that emits ultraviolet light. After that, you can begin casting with UV resin. A good UV light kit contains a UV resin vaporizer, casting molds, color pigments, and utensils for mixing the colors.
UV resins are a great choice if you need to quickly apply a durable finish to a large surface. This type of resin has a higher shelf life and doesn’t require UV lamps. As an added bonus, it won’t need to be reapplied as often. You can also find UV resins in large-sized bottles for greater storage. But if you’re using UV resins in your DIY projects, consider investing in larger containers of the UV resin. You will be glad you did!